News
Optimizing Manufacturing with Core Model MES | Innovative Solutions
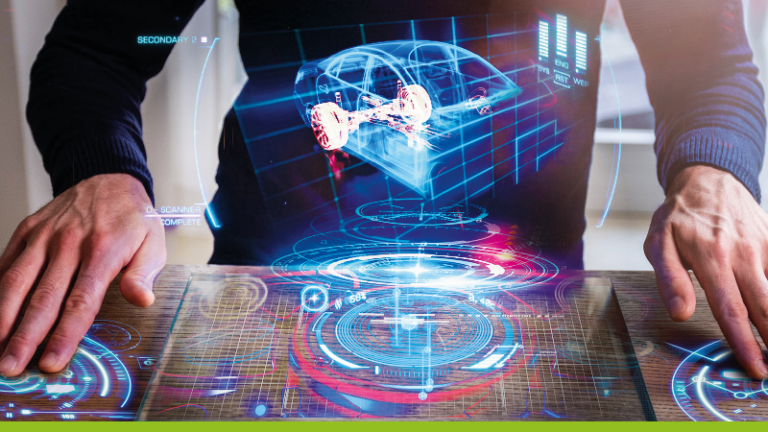
In the competitive landscape of modern manufacturing, organizations are constantly seeking ways to enhance efficiency, reduce costs, and improve product quality. One of the most effective strategies to achieve these goals is through the implementation of a Manufacturing Execution System (MES) using a Core Model approach. This methodology not only streamlines processes but also ensures that best practices are standardized across multiple sites. In this blog post, we’ll explore the benefits of the Core Model, address common challenges, and share best practices for successful implementation.
Blogpost outline :
- Understanding the Core Model Approach
- The Game-Changing Impact on Industrial Performance
- Governance and Non-Regression Testing in MES Implementation
- Expert Insights from Sofyne’s MES Solution Architects
- Best Practices for Core Model Implementation
- Use cases from our customers
Understanding the Core Model Approach
The Core Model approach involves designing and deploying a cutting-edge MES solution at the group level, followed by an efficient rollout to different sites within a company. This centralized strategy utilizes advanced tools and architecture to create a cohesive solution that can be distributed across all factories.
The primary objectives of this approach include:
- Standardizing Best-in-Class Processes: By implementing a Core Model, organizations can ensure that each factory adheres to the same high standards, resulting in consistent quality and efficiency.
- Rapid and Cost-Effective Deployment: A well-defined Core Model allows for quicker deployments across multiple locations, reducing the time and resources required for each rollout.
- Improving Total Cost of Ownership (TCO): By standardizing technology and processes, companies can significantly lower their TCO for manufacturing information systems.
The Game-Changing Impact on Industrial Performance
Implementing a Core Model for MES is a game-changer for optimizing industrial performance. This holistic approach not only streamlines operations but also fosters a culture of continuous improvement. Organizations can leverage the experiences of others through user clubs, where customers who have adopted the Core Model share insights and testimonials.
These discussions often highlight challenges faced by IT and operational departments, such as:
- The difficulties in understanding and standardizing processes across the organization.
- The day-to-day responsibilities of internal Core Model champions who drive the initiative.
Governance and Non-Regression Testing in MES Implementation
Effective governance is the backbone of any successful MES implementation, especially when adopting a core model approach. Establishing a clear governance framework ensures alignment between business objectives, technical configurations, and operational requirements across all project phases. To safeguard the core model’s integrity during updates or releases, non-regression testing, preferably through automated test suites, becomes essential. Automated testing accelerates validation cycles, reduces manual errors, and provides consistent assurance that new developments do not inadvertently disrupt existing functionalities. By integrating governance practices with robust test automation, organizations can foster a scalable and resilient MES environment, enabling seamless adaptations to future needs while maintaining system reliability and compliance.
Expert Insights from Sofyne’s MES Solution Architects
Sofyne’s team of MES solution architects have extensive experience in navigating the complexities of implementing a Core Model. They emphasize the importance of avoiding common pitfalls, such as:
- Lowering the need for thorough process documentation and analysis before deployment.
- Failing to engage relevant stakeholders during the design and rollout phases.
- Poor governance frameworks lead to inconsistent decision-making, uncontrolled deviations from the core model, and escalating maintenance costs.
- Overlooking the importance of training and support for factory personnel.
Best Practices for Core Model Implementation
To maximize the success of a Core Model implementation, consider the following best practices:
Start with a Pilot Site
Establish a Strong Governance Model
Foster Collaboration
Design the factories must-have & nice-to-have
|
Adapting to Agility
The Core Model is designed to be flexible and responsive, ensuring that it can adapt to support operational excellence. This dynamic model evolves iteratively to meet changing needs, making it a transformative solution for optimizing industrial processes and governance.
Here are some key considerations:
- Continuous Improvement: Regular evaluations of the Core Model’s effectiveness and its alignment with business objectives will help identify areas for enhancement.
- Integration with Existing Systems: Ensuring compatibility with current software packages is crucial to avoid disruptions and maximize the return on investment.
- New Factory Roll-Outs: As new factories come online, the Core Model can be seamlessly adapted, ensuring that they benefit from the established best practices from the outset.
DELMIA Apriso MES: The perfect fit for the Core Model Approach
One of the standout solutions for implementing a Core Model is DELMIA Apriso MES. Its native standard modules and easy deployment capabilities make it particularly well-suited for this approach. Companies can leverage its robust functionalities to create a unified manufacturing execution strategy that aligns with their operational goals.
In today’s fast-paced manufacturing environment, adopting a Core Model approach for your MES implementation can yield significant benefits. By standardizing processes, streamlining deployments, and improving total cost of ownership, organizations can enhance their industrial performance and foster a culture of continuous improvement. Engaging with experts like Sofyne can provide the necessary guidance to navigate this transformative journey successfully.
As you consider implementing a Core Model for your MES solution, remember to embrace agility, foster collaboration, and continuously refine your processes. By doing so, you will not only optimize your operations but also position your organization for sustained success in the competitive manufacturing landscape.
Customers Use Cases
#1 – Automotive industry use case
The automotive industry provides a compelling example of the successful implementation of a core model approach. One leading automotive manufacturer developed two distinct core models: one for its MES (Manufacturing Execution System) focused on production and another for its WMS (Warehouse Management System) tailored to logistics.
These core models were designed to:
The deployment strategy allowed for:
Key governance elements included:
This approach not only optimized production and logistics but also fostered a culture of standardization and continuous improvement across the organization, reinforcing its competitive edge in a fast-paced industry. |
#2 – Nuclear industry use case
The nuclear industry presents another powerful example of leveraging a core model approach. A leading nuclear company developed a core model by taking the most functionally complex site as a reference.
The approach was designed to:
The deployment process included:
This strategic approach not only streamlined operations but also provided the flexibility to address site-specific challenges, ensuring regulatory compliance and operational efficiency across the entire organization. |
MES Core Model approach unlocks Manufacturing transformation
![]() |
Partner with Sofyne and embark on a journey towards optimized factories with a MES Core Model. |
![]() |
Contact us to learn more about how we can help you achieve your factories digitization project |
Useful links
- Factory of the Future | DELMIA – Dassault Systèmes : www.3ds.com/factory-of-the-future/
- MESA.org | History of the MESA Models : www.mesa.org